“What’s nice about concrete is that it looks unfinished” – Zaha Hadid
Concrete is all about being creative. But your creativity does not have to stop with the design of the concrete structure…
I have always been fascinated with the process of forming 3-dimensional shapes using 2-dimensional elements. Inspired by works like Cirrus by Zaha Hadid, I came upon the idea to construct formwork for a vaulted concrete roof using the ‘flat-pack’ concept. In this first blog in my new Concrete Blog Series, I go through the process of how I built this vaulted concrete roof using ‘flat-pack’ formwork.
The Brief
The brief was simple, build a 7.5m x 5m library with a vaulted concrete roof, on a property down a panhandle, with trees big enough that it probably dates from my grandfather’s youth, in the middle of Sandton. So access was limited to say the least. With no overhead space for a crane or a concrete pump, everything had to be taken to site by hand only.
Problems!
Initially, I went the traditional route, without thinking about it too much, until I received the first proposal from a formwork supplier, and I realized that maybe I have a problem.
The best offer I could get from a formwork supplier was pre-built panels, of which the smallest section would weigh 175kg. There was just no way I would be able to get the formwork into position by hand and even getting a small crane in was out of the question. I considered assembling this formwork in position on top of a formwork deck but due to the complexity of assembling formwork like this, it was just not an option.
Then there was the cost. The total cost for supply only of this ‘traditional’ formwork was R 82 000. For a small project like this, the formwork cost would have made it completely not viable. At this point, nothing was working out and I knew I had to start thinking out of the box to come up with a solution.
Getting Creative
With my fascination with ‘flat-pack’ furniture and ‘ribbed’ architecture, I began wondering if it would be possible to form the vault with a ‘flat-pack’ ribbed structure. After a few hours of playing around with concepts, I came up with a structure that looked like it could work.
At this point, I had a solution for the internal structure, but concrete needs a closed mould, or so I thought. I decided to contact a friend of mine who is a concrete technologist for one of the big ready-mix suppliers. After some head-scratching and tossing ideas around I suddenly saw his face lit up as he announced; “Let’s pack it like a swimming pool!”, and the rest was history.
It took some convincing to get the project engineer on board but eventually, he bought into the concept, and I set out designing the system.
The Design
The success of the system was going to be dependent on getting two main things right. The first was the assembly of the formwork in terms of accuracy and ease of assembly. To achieve this, the ‘flat-pack elements’ were slotted in such a way that with the use of spacers, the structure could be assembled without even the need for a tape measure. So the accuracy and ease of assembly were designed into the flat-pack boards. Assembly was literally ‘plug and play’.
The second was to be able to pack the concrete accurately on top of this vaulted tube to an even thickness throughout and to a proper half-circle shape to the outside of the dome. To achieve this, templates were cut with the rest of the structure elements, to be used as guides during the placing of the concrete.
The following diagram shows how the ‘flat-pack’ would be assembled and cladded to form the vault formwork. The material that was to be used was a normal grade 19mm shutter board for the ribs and spacers. 76×50 SAP profiles were to be inserted into pre-cut slots to work as ‘purlins’ for the fixing of 0,8mm galvanised sheets for the final cladding.
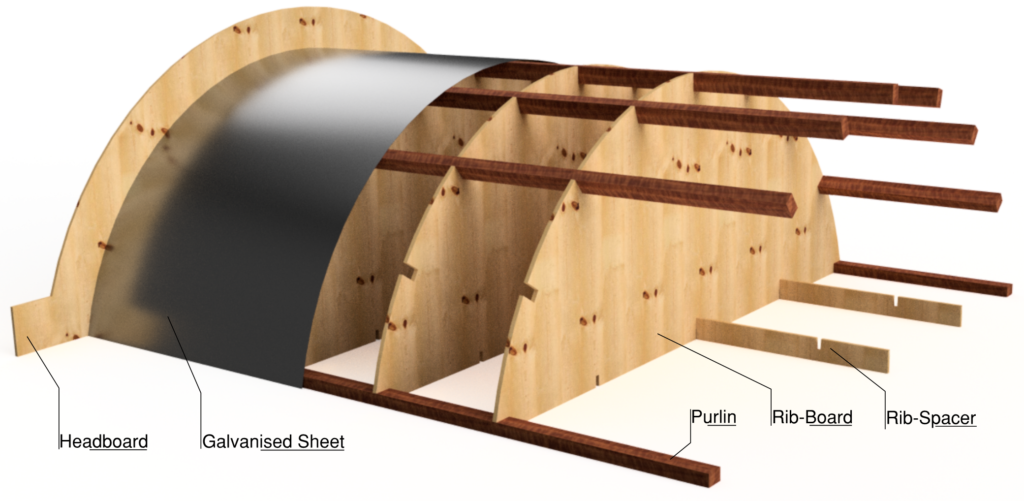
Construction
The first step was to cut the shutter board profiles. This was done using water jet cutting. Shutter board survives this process quite well provided the boards are allowed to dry out properly after cutting. Below is the cutting layout that was used to cut the boards.
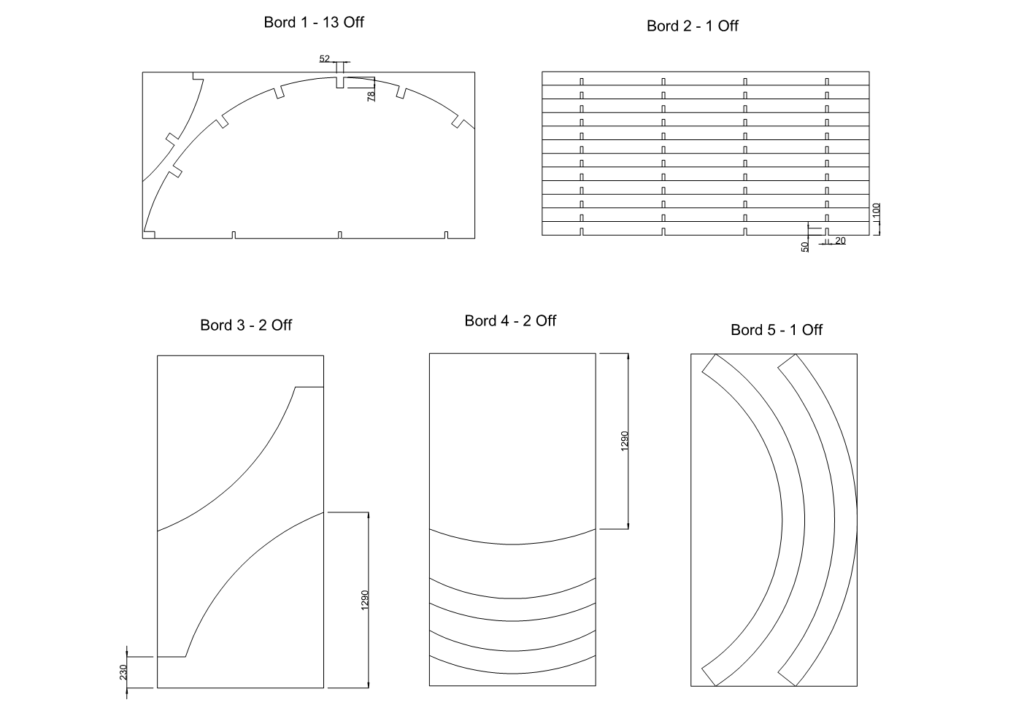
The base of the vaulted formwork was shuttered with boards as for a normal roof slab with the vaulted formwork erected on top of the flat shuttered surface. A picture is worth a thousand words so without any further explanations, follow the rest of the construction process through the following photos.
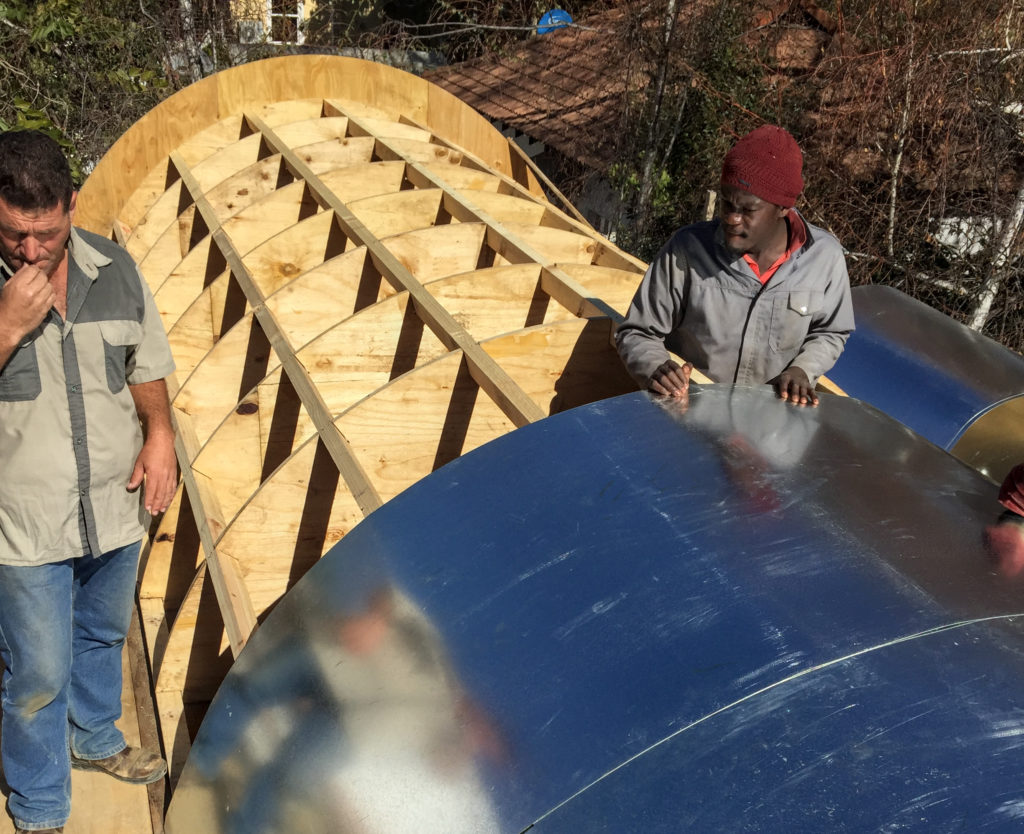
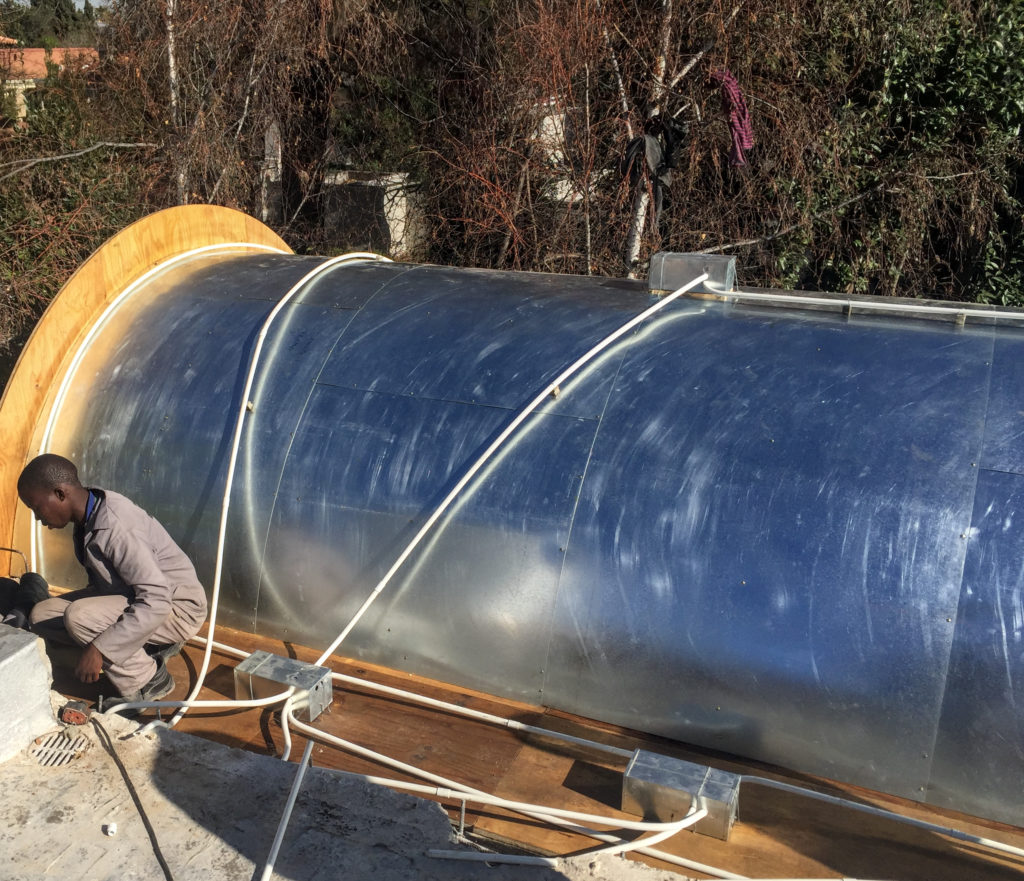
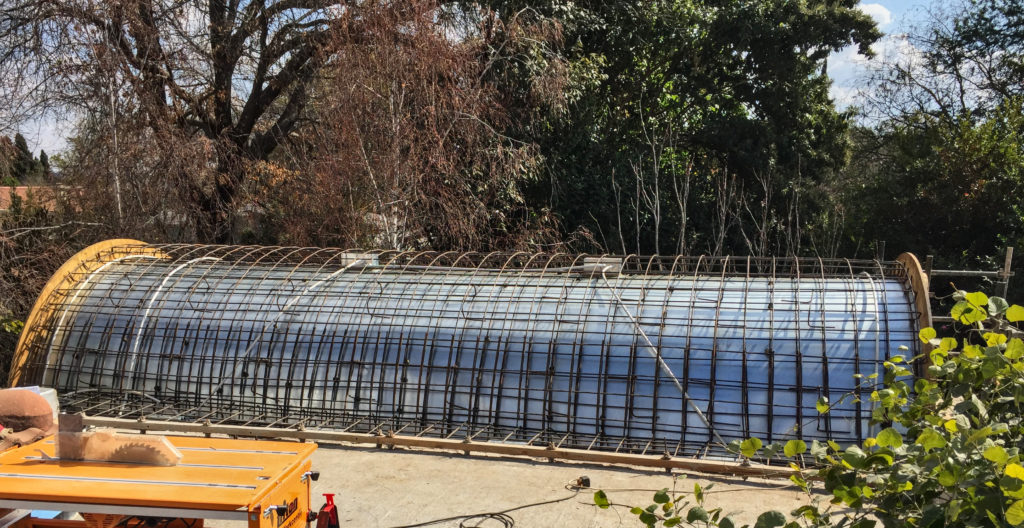
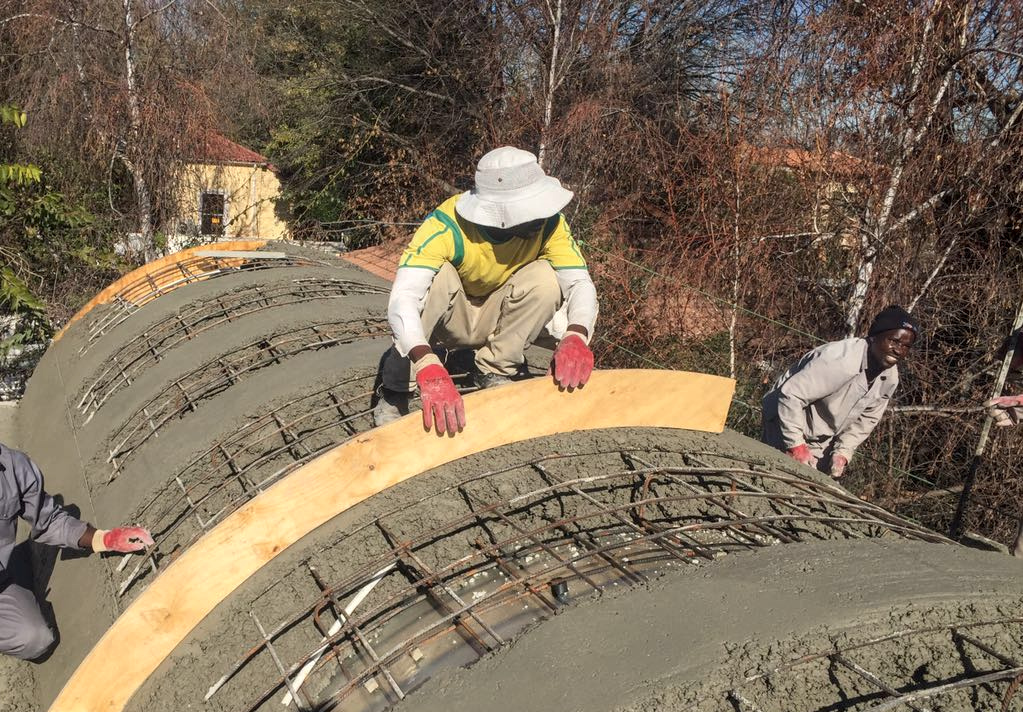
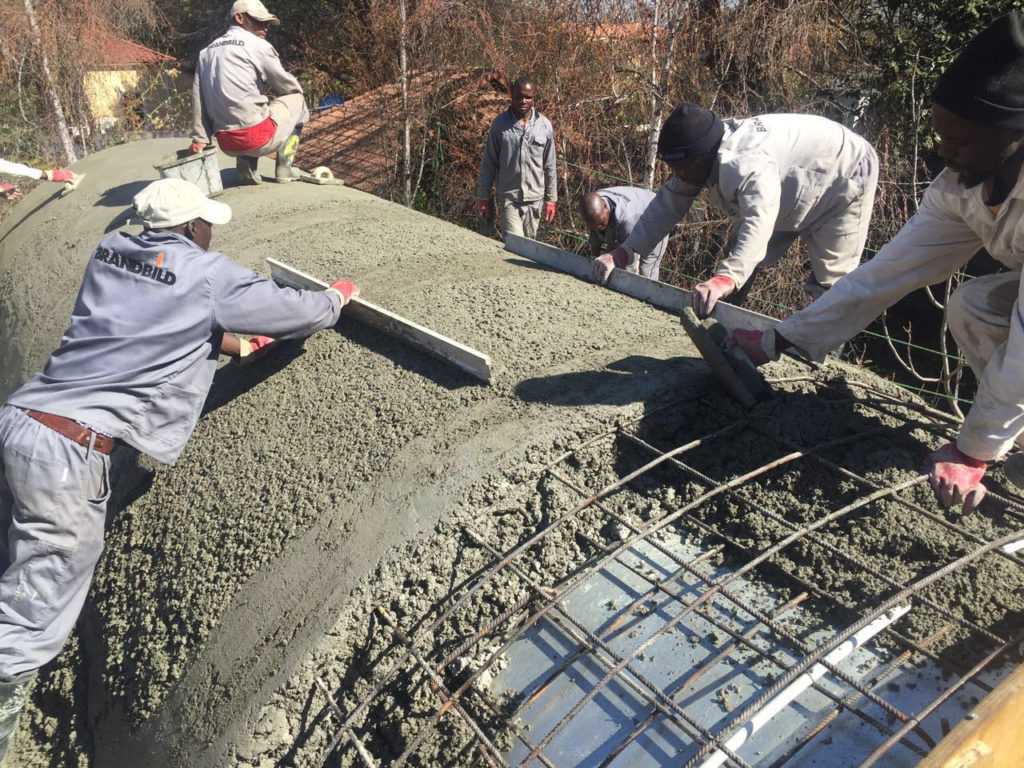
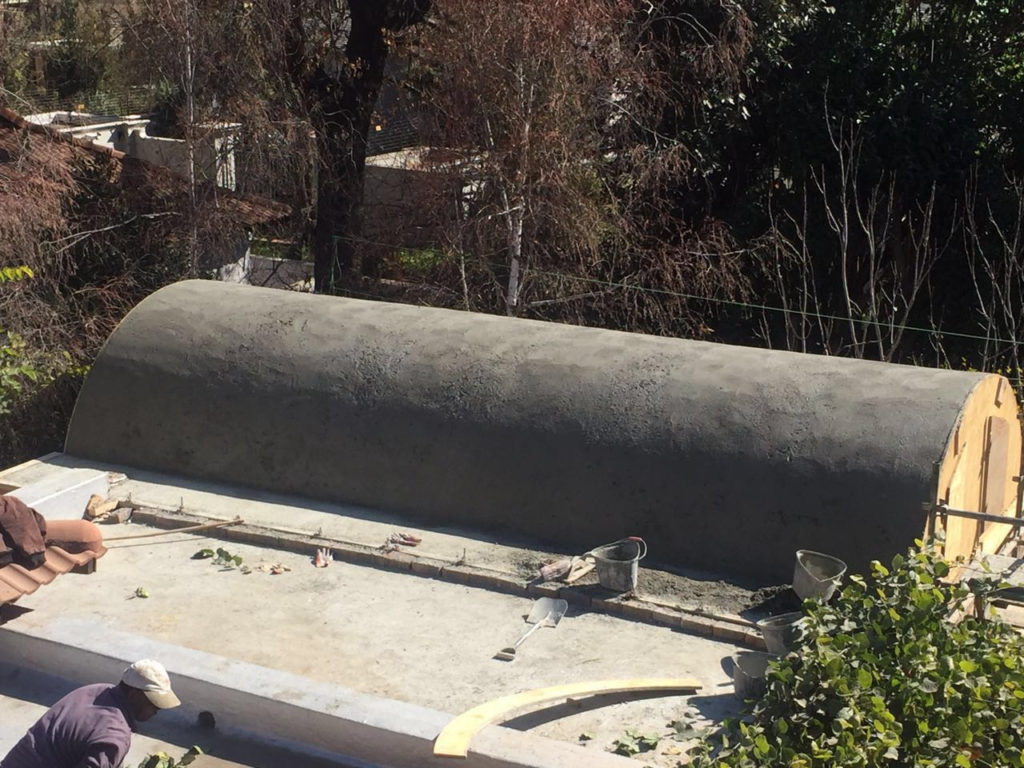
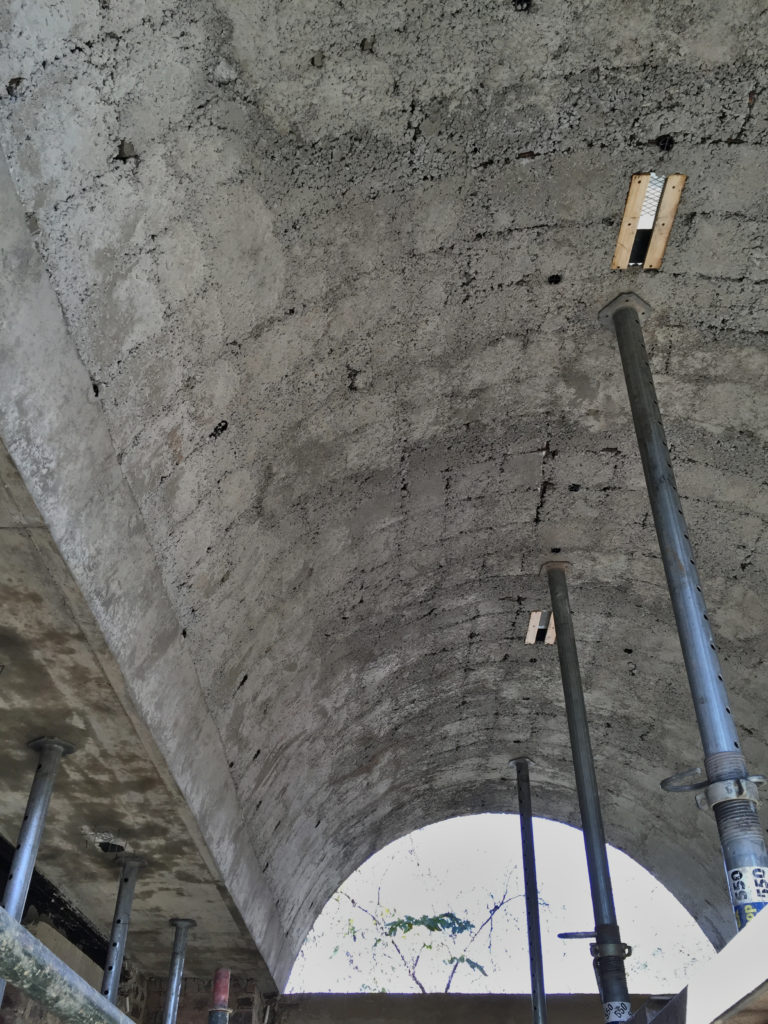
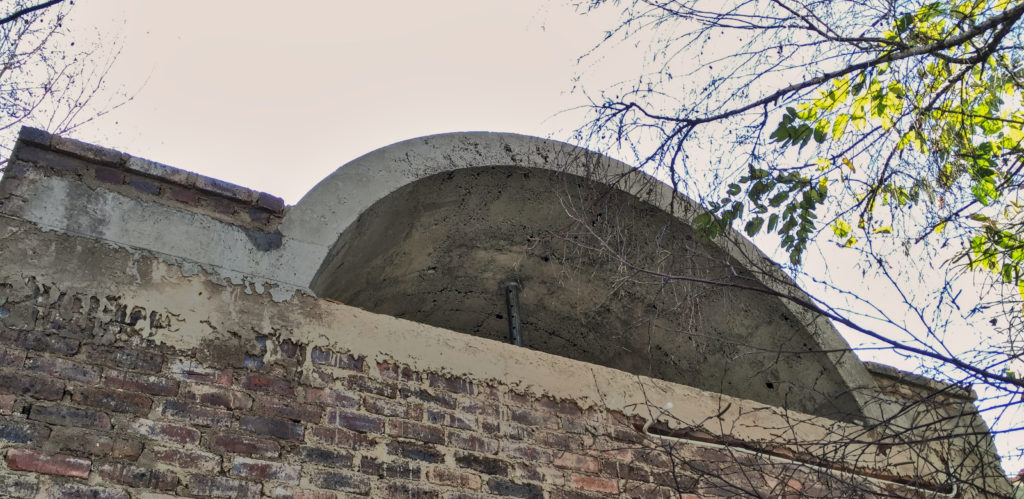
What happened with the budget problem?
The total cost for the ‘flat-pack formwork’ came to R 22 500 including the water jet cutting which was a 75% saving on the cost for ‘traditional’ formwork. Other than the cost-saving on the formwork, since there were no cranage and concrete pumping involved, this resulted in further cost savings.
So, what will you do?
My purpose with this blog is to illustrate what can be done using alternative formwork methods. And illustrating that the possibilities do not stop with just using alternative formwork but also with what can be achieved by using different concrete mixes.
I hope this blog inspires you, when you design your next amazing concrete structure, to think of new forms, new applications, and new solutions for old problems.
Let me know in the comments below of alternative applications for ‘flat-pack formwork’ that you can think off.
Should you require any assistance with your next concrete project or would like to get more information on our moulded concrete solutions, feel free to contact me at anton@elemento.net.za